Unlock 302 Rocker Arm Torque Specs for Optimal Performance
The torque spec for a 302 Rocker Arm is 50-58 in-lbs.
302 Rocker Arm Torque Specs
Understanding the proper rocker arm torque specs for your 302 engine is essential in ensuring your engine functions properly and to prevent any potential damage or engine failure. Knowing the torque specs can go a long way in prolonging your motors life. When adjusting and applying torque to your 302 rocker arms, be sure to follow the manufacturers recommended specifications. This will ensure peak performance is sustained and, ultimately, that maximum power is attained. The torque spec for 302 rocker arm nuts typically ranges from 10 to 12 ft-lbs, while the rocker arm studs are typically torqued between 18 and 22 ft-lbs. There may be slight variations depending on the particular engine model, so be sure to consult your owner’s manual or a trusted professional for accurate specs. Once you’ve properly tightened each nut and stud to the specified torque, you can be assured that your vehicle will operate at its peak performance level for some time.
Requirements for Torque Specs
Torque specifications for 302 rocker arms are detailed in the engine manufacturer’s manual. Depending on the engine, the torque specs may vary. Generally, they are determined by the type of rocker arm being used and its material composition. The specs will also depend on the application of the rocker arm, such as whether it is being used in a drag race or a street car. It is important to always adhere to the manufacturer’s specifications when torquing rocker arms. Failure to do so may result in inadequate clamping force, which can lead to serious engine damage.
Tools for Torque
The most commonly used tool for accurately torquing 302 rocker arms is a torque wrench. A torque wrench is a specialized tool that is designed to measure and apply force with precision. It consists of a handle, dial indicator and spring-loaded mechanism that measures and applies force with accuracy up to a certain level, usually around 100 ft-lbs (pound-feet). When using a torque wrench, it is important to double check that it is correctly calibrated and set prior to use.
Types of Rocker Arms
There are several types of rocker arms available for different engines. Solid lifter rockers are made from one piece of metal and provide good clamping force but require more frequent adjustments than other types of rockers. Hydraulic roller lifters are made from multiple pieces that are connected by springs and provide excellent clamping force while requiring less frequent adjustments than solid lifters. Adjustable roller lifters allow you to adjust both valve lash and spring pressure with ease while providing excellent clamping force similar to hydraulic roller lifters. Lastly, pedestal mount lifters are unique in that they sit higher off the cylinder head than other types of lifters, allowing them to provide better leverage during acceleration or high RPMs while still providing adequate clamping force.
Benefits of Proper Torque Specs
Adhering strictly to proper torque specs when torquing 302 rocker arms can provide numerous benefits for your engines performance and longevity. Properly torqued rockers will ensure adequate clamping force on the valve stem which helps reduce friction between components and improve engine efficiency by allowing valves to open more quickly without wasting energy on additional friction between components. Additionally, properly torqued rockers will prevent premature wear caused by too much or too little tension which can lead to excessive valve stem wear or even catastrophic failure if left unchecked over time. Finally, properly torqued rockers can also improve fuel economy as well as overall drivability due to improved valve timing accuracy which helps keep your vehicle running smoothly no matter how hard you push it!
Importance of Proper Rocker Arm Torque Specs
The importance of adhering strictly to proper torque specs for 302 rocker arms cannot be understated given their crucial role in an engines performance and longevity. Not only do properly torqued rockers reduce friction between components resulting in improved efficiency but they also help prevent premature wear caused by too much or too little tension which can lead to serious damage over time if left unchecked. Furthermore, properly torqued rockers also help improve fuel economy as well as overall drivability due to improved valve timing accuracy which keeps your vehicle running smoothly no matter how hard you push it! For these reasons, its essential that you always adhere strictly to the manufacturer’s specified torque specs when installing new 302 rocker arms into your vehicles engine!
Determining Rocker Arm Torque Specs
When it comes to determining rocker arm torque specs, there are several factors that must be taken into consideration. First, the size of the bolt is important, as this will determine the amount of torque that is applied to the rocker arm. Additionally, the material used for the bolt must be considered, as different materials require different levels of torque. Additionally, the engine type and size should also be factored in when determining rocker arm torque specs.
In order to ensure that all bolts are properly torqued and seated correctly, it is important to use a torque wrench when tightening them. This will help ensure that each bolt is tightened properly and with even tension so that no part of the engine is over or under-torqued. Additionally, it is important to use a torque specification chart when setting up rocker arm torque specs so that all bolts are tightened to their recommended levels.
Choosing the Right Size Bolt for Rocker Arm Torque Specification
When choosing which size bolt to use for a rocker arm torque specification, it is important to consider both safety and performance. Generally speaking, larger bolts are more secure and less likely to cause damage due to over-torquing. However, larger bolts may not fit in all applications or may require special tools for installation. It is therefore important to consult with a professional before choosing an oversized bolt for any application.
Furthermore, different materials require different levels of torque in order to provide adequate performance and protection from damage due to over-torquing. It is therefore important to select a bolt with appropriate material properties in order to get optimal results from any application requiring a rocker arm torque specification.
Questionable Variables When Setting Up Rocker Arm Torque Specifications
When setting up rocker arm torque specifications there can be many variables that must be taken into consideration such as engine type and size; material used for bolts; and size of bolts chosen for application. Additionally, if any additional components are added such as gaskets or washers they can also affect the level of tension required on each bolt which can contribute significantly towards how tight they need to be torqued down in order to ensure optimal performance from your engine.
It is therefore important to consult with a professional prior to attempting any adjustments or modifications on your engine so that you know exactly how tight each individual component should be torqued down in order achieve optimal performance without causing damage or risking safety issues due improper tightening techniques or excessive force applied when torquing down components beyond their recommended levels.
Correct Seating and Processes When Working With Rocker Arm Torques Specification
Once all variables have been taken into consideration and an appropriate size bolt has been chosen for your application its time begin seating components correctly during installation process when working with rocker arm torques specifications. This includes ensuring that all nuts and washers are properly aligned before any force has been applied during installation process as well as making sure that all gaskets have been installed correctly so that no air gaps exist between them which could lead excessive wear on components due improper seating techniques being employed during installation process stages .
Additionally its also important make sure each nut has been properly greased prior being placed onto threads on each individual component so they dont bind together during installation process which can cause excessive force being applied on components leading too dangerous situation if too much pressure has been applied by technician during installation process stages . Finally , once seating positions have been confirmed it’s then time start applying correct amount of tension during installation process using an appropriate sized wrench , as this will help ensure each component has been tightened correctly while providing optimal performance levels from your engine without risking any safety issues due improper tightening techniques being employed .
FAQ & Answers
Q: What are the requirements for torque specs?
A: The requirements for torque specs depend on the type of rocker arm being used, as different types require different amounts of torque to secure them properly. It is important to check the manufacturers specifications prior to beginning any work, as over-tightening or under-tightening can cause damage to the engine.
Q: What tools are needed to apply torque specs?
A: A torque wrench is needed to apply the proper torque specs. The size of the wrench should match the size of bolt being used, and it should be calibrated regularly in order to ensure accurate readings.
Q: What types of rocker arms are there?
A: There are several types of rocker arms available, including hydraulic roller rocker arms and solid roller rocker arms. Each type has its own unique characteristics and should be chosen based on the engines needs and performance requirements.
Q: What are the benefits of proper torque specs?
A: By using proper torque specs when installing a rocker arm, you can ensure that it is secured properly and will not become loose over time. Using too little or too much torque can cause damage to both the engine and the part itself, so it is important to get it right. Properly torqued components also increase efficiency and help prevent wear on other parts in the system.
Q: How do I determine proper rocker arm torque specs?
A: To determine proper rocker arm torque specs, check with your vehicles manufacturer or consult an automotive technician for advice. Many online resources also provide information on what those specifications should be for various vehicle makes and models. It is important to use only reliable sources when determining these specifications as incorrect information could lead to damage or reduced performance from your engine.
The 302 rocker arm torque specs for a standard production engine will vary depending on the make and model, however the general range is typically between 15-20 ft/lbs. It is important to ensure that the torque specs are properly followed to ensure proper performance of the engine, as an incorrect setting can lead to severe damage.
Author Profile
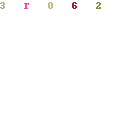
-
Welcome to Liberty Is Viral, a digital nexus where curiosity is the currency and knowledge is the merchandise. We are not just another blog on the block; we are a movement, a collective of inquisitive minds committed to the ethos of liberating information and empowering individuals.
Our journey began with a simple yet profound belief: knowledge should be accessible to all, unrestricted by barriers, free as the air we breathe. Thus, in the bustling digital landscape of 2023, LibertyIsViral.com was reborn, a revitalized platform poised to quench the intellectual thirst of discerning netizens. And we can say we are a bit successful on that, since our community is expanding by the day (20,000 readers and increasing!)
Latest entries
- March 22, 2023AppliancesThe Best 2 Inch Brass Fire Hose Nozzle for Maximum Firefighting Efficiency
- March 22, 2023AppliancesElevate Your Brand with the Best Custom Next Service Due Stickers
- March 22, 2023Lawn, Patio And Exterior5 Best Bird Netting Solutions for Protecting Cherry Trees
- March 22, 2023Apparel And JewelryFind the Best Drop Cut T-Shirt for Men: Our Top Picks