What is the Correct 6.0 Injector Hold Down Torque for Maximum Performance?
The proper torque for 6.0 injector hold down bolts is 12-14 ft-lbs.
6.0 Injector Hold Down Torque
The 6.0 Injector Hold Down Torque is the amount of force required to keep fuel injectors in place on a 6.0-liter engine. This is important because it must be high enough to ensure a reliable and efficient performance from the engine. Too little torque and the injectors may vibrate and be unstable; too much torque can damage them or cause cylinder misfiring. Installing injectors requires care when tightening to ensure proper torque is applied, otherwise it can lead to costly engine repairs or issues later down the line. To ensure optimal performance, it’s essential that the proper torque for a 6.0-liter engine is used; this ranges from 45-60 placed pounds, with variations depending on specific make and model of engine.
Engine Injectors
Engine injectors are devices that are used to control the flow of fuel and air into an engine. They are typically found in internal combustion engines, such as those found in cars and trucks. The injectors are responsible for delivering a precise mixture of fuel and air to the engine at the correct time, allowing for optimal performance. There are several types of injectors, including direct injection (DI), port injection (PI), and diesel fuel injection (DFI). Each type has its own unique set of parts and functions.
Direct injection systems allow fuel to be injected directly into the combustion chamber, while port injection systems use an intake manifold or other component to deliver the fuel-air mixture. Diesel fuel injectors are used in diesel engines and work differently than gasoline injectors. They use high-pressure pumps to deliver a fine mist of fuel directly into the cylinders at a precise time, allowing for improved efficiency and performance in diesel engines.
The Need for Proper Injector Hold Down Torque
In order to ensure that the injector is securely fastened to its mounting surface, it is important to use proper injector hold down torque when installing or replacing an engine injector. Insufficient torque can cause the injector to become loose over time, leading to increased exhaust gas leakage and reduced power output from the engine. Over torquing can also be detrimental, as it can cause threads on the mounting surface or screws to strip out or become damaged over time.
Factors Affecting Injector Hold Down Torque
When selecting an appropriate torque setting for an engine injector hold down bolt, there are several factors that must be taken into consideration. The first is the quality of the threads on both sides of the screw. If they are worn out or damaged in any way, then it may not be possible to achieve a proper torque setting without damaging them further. Another factor is the quality of the pressure plate that holds down all four corners of the injector assembly; if it is too thick or too thin then it may not provide enough compression force on the screws when they are tightened down properly.
Injector Removal and Installation Procedure
The procedure for removing and installing an engine injector will vary depending on make and model of vehicle but there are some general steps that should always be followed when performing this task:
1) Gather required tools such as socket wrenches, flathead screwdriver, spark plug wrench/socket etc.;
2) Disconnect all electrical connections from the injector;
3) Unscrew all bolts holding down pressure plate;
4) Carefully lift off pressure plate;
5) Unscrew hold-down bolts from sides of mounting surface; 6) Lift off old injector assembly; 7) Clean mounting surface with brake cleaner; 8) Place new injector assembly onto mounting surface; 9) Reinstall hold-down bolts with proper torque settings; 10) Place back pressure plate onto mounting surface with proper torque settings; 11) Reinstall electrical connections onto new assembly; 12) Start engine and check for proper operation before driving vehicle again.
Attempts To Tighten An Injector Hold Down
In order to tighten an already installed engine injecotr hold down bolt properly without having access to a full size torque wrench, two methods can be employed: using a scissor jack or using a motorcycle stand. Both methods involve placing two objects together in order to create enough friction between them so that when tightened by hand they will create enough tension on either side of a bolt and nut combination that will approximate factory specified torque levels without damaging any components involved in process . Using either one requires patience and knowledge about what amount of force each item can take before being damaged permanently so caution must be taken when attempting this method .
Resetting the Injectors Circuit
Resetting the injectors circuit is an important step in ensuring that all the components are functioning properly. The first step is to check the fuse and relays to make sure they are in good working order. If either of these components are not functioning, it can cause issues with the injectors performance. If there is a problem with either of these components, they should be replaced or repaired before reinstalling the injector.
Inspections Before Reinstallation of The Injectors
Before reinstalling the injectors, it is important to perform visual inspections and electrical connection checks. This ensures that all components are in good working order and that there will be no problems with performance once the injectors are reinstalled. Visual inspections should include inspecting for any corrosion or damage, such as cracks or holes in any of the components. Electrical connections should also be checked for proper connections and any loose wiring should also be tightened up before reinstallation.
Tips on the Proper Injection Hold Down Torque
When installing an injector hold down torque, it is important to follow some general guidelines on torque requirements. Generally speaking, it is recommended to use a torque wrench when tightening down screws and bolts on an injector hold down torque so that an even pressure can be applied throughout the entire process. It is also important to keep track of how much torque has been applied so that too much pressure isn’t applied which could lead to damage or malfunctioning of components.
Replacing Parts of an Injector Hold Down
When replacing parts of an injector hold down, it is important to use quality pressure plates and screws for replacement. Using quality parts helps ensure that the job will last for a long time without having any issues with performance or functionality due to poor quality parts. Additionally, using quality screws helps ensure that there won’t be any issues with stripping or breakage due to too much tension being applied during installation or removal of parts from an injector hold down.
FAQ & Answers
Q: What types of engine injectors are there?
A: There are two main types of engine injectors: direct-injection and port-injection. Direct injection injects fuel directly into the combustion chamber, while port injection injects fuel into the engine’s intake manifold.
Q: What is the need for proper injector hold down torque?
A: Proper injector hold down torque is necessary to ensure a secure connection between the injector and the engine in order to prevent performance loss or damage to components due to leakage. Insufficient torque can lead to loosening of the connection, while over-torqueing can strip or crack threads on the screws.
Q: What factors affect injector hold down torque?
A: The quality of the pressure plate and the threads of the screws can both affect the amount of torque required for a secure connection. If either are damaged they may require more torque than usual in order to be secured properly.
Q: What is the procedure for removing and installing an injector?
A: The procedure for removing and installing an injector requires several tools such as a ratchet, socket, screwdriver, and wrench. It also requires several steps such as disconnecting electrical connections, loosening bolts holding down the pressure plate, and removing any other components obstructing access to the injector before replacing it with a new one or re-installing it after repairs have been made.
Q: What tips should be followed for proper injection hold down torque?
A: General guidelines on torque requirements should be followed closely when tightening screws on an injection hold down plate in order to ensure proper sealing between components. Additionally, techniques such as alternating between screws can help ensure even tightening across all screws and reduce risk of leakage due to uneven pressure.
Overall, the 6.0 Injector Hold Down Torque is an important part of the engine’s performance and should be taken seriously. Having the proper torque for the injectors will ensure that your engine runs smoothly and efficiently without any problems. It is recommended that you refer to your vehicle’s manual for exact specifications and use a torque wrench to get the best results. Following these guidelines will keep your engine in top running condition for years to come.
Author Profile
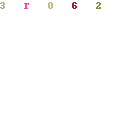
-
Welcome to Liberty Is Viral, a digital nexus where curiosity is the currency and knowledge is the merchandise. We are not just another blog on the block; we are a movement, a collective of inquisitive minds committed to the ethos of liberating information and empowering individuals.
Our journey began with a simple yet profound belief: knowledge should be accessible to all, unrestricted by barriers, free as the air we breathe. Thus, in the bustling digital landscape of 2023, LibertyIsViral.com was reborn, a revitalized platform poised to quench the intellectual thirst of discerning netizens. And we can say we are a bit successful on that, since our community is expanding by the day (20,000 readers and increasing!)
Latest entries
- March 22, 2023AppliancesThe Best 2 Inch Brass Fire Hose Nozzle for Maximum Firefighting Efficiency
- March 22, 2023AppliancesElevate Your Brand with the Best Custom Next Service Due Stickers
- March 22, 2023Lawn, Patio And Exterior5 Best Bird Netting Solutions for Protecting Cherry Trees
- March 22, 2023Apparel And JewelryFind the Best Drop Cut T-Shirt for Men: Our Top Picks