How to Properly Adjust the Injector Hold Down Bolt Torque for 7.3 Engines
The injector hold down bolt torque should be tightened to 34 foot-pounds.
7.3 Injector Hold Down Bolt Torque
Injector Hold Down Bolt Torque is the process of tightening fasteners, such as nuts and bolts, to a specific torque. Its purpose is to ensure that the specified clamping force is achieved to securely hold two parts together. The torque that is applied must not exceed the recommended torque in order to avoid damaging the joint or causing fatigue failure due to over-tightening. Ensuring that proper torque is applied helps maintain consistent performance of an engine for many years.
7.3 Injector Hold Down Bolt Torque
The torque specifications for an injector bolt are extremely important in order to ensure the proper functioning of the fuel delivery system, and to avoid engine damage. The various types of bolts and their respective torque settings can differ greatly, depending on whether they are made from steel or aluminum. It is essential to adhere to the manufacturer’s recommended torque specifications in order to maintain the optimal performance of the engine.
Types of Injector Bolts
Steel and aluminum are two of the most common materials used for injector bolts, but other types may also be available depending on the make and model of vehicle. Steel bolts tend to be stronger and more durable than aluminum, making them a better choice for high-performance vehicles that require a greater degree of power output. Aluminum bolts, on the other hand, are lighter and more corrosion-resistant, making them ideal for everyday driving conditions.
Torque Settings
The proper torque settings must be followed in order to secure an injector bolt properly. Too little torque can lead to a loose connection between the bolt and its components, while too much torque can cause damage to both the components and the bolt itself. Depending on the type of injector bolt being used, different torque settings may be recommended by manufacturers or repair manuals.
Reasons To Maintain Injector Hold Down Bolt Torque
In order to ensure proper functioning of a fuel delivery system and overall engine performance, it is important that all injector hold down bolt torques are correctly set according to manufacturer recommendations. If too little or too much torque is applied during installation or maintenance procedures, it could lead to problems such as decreased engine power output or even engine damage if left unchecked over time. Additionally, if a fuel delivery system is not operating optimally due to incorrect installation or maintenance procedures it could lead to reduced fuel efficiency as well as increased emissions levels from exhaust gases.
Procedures For Torque Measurement
In order to accurately measure the correct amount of torque being applied during installation or maintenance procedures it is necessary that all tools used in these processes are calibrated correctly first. This involves adjusting manual wrenches so that they provide consistent readings when tightening or loosening nut fasteners as well as calibrating digital tools such as electronic dial indicators so that they provide accurate readings when measuring angles or forces between components. It is also important that all components being measured have their measurements double-checked beforehand in order to ensure accuracy during calibration processes.
Common Used Tools for Injector Hold Down Bolt Torque Measurement
In order to ensure proper and safe tightening of the bolt, it is important to use the right tools. The commonly used tools for this purpose are a manual wrench and a digital gauge. A manual wrench is used to apply the required pressure on the bolt while the digital gauge helps in measuring the torque applied on it. Both these tools help in ensuring that the bolt is tightened properly and safely.
Steps to Follow While Tightening the Bolt
The steps that need to be followed while tightening an injector hold down bolt include ensuring proper gapping between the components, applying proper pressure using a tool such as a manual wrench, and measuring the torque applied with a digital gauge. It is important to make sure that all these steps are followed in order to ensure that the bolt is tightened safely and accurately.
Benefits of Properly Tightened Injector Bolts
The main benefit of properly tightening an injector hold down bolt is protection of genuine spare parts from wear and tear due to excessive vibration or movement. Additionally, a properly tightened bolt also ensures better performance and reliability from your engine as it helps reduce friction and heat buildup in your engine.
How To Keep Track Of Injector Hold Down Bolt Replacement
Keeping track of injector hold down bolt replacement can be done easily by keeping maintenance logs or records in computer database systems. This will allow you to keep track of any changes or replacements made, as well as when they were made so you can reference them at any time. Additionally, it also makes it easier for mechanics to quickly identify any potential issues before they become more serious or costly repairs down the line.
FAQ & Answers
Q: What types of Injector Bolts are used? <\N>
A: Generally, steel and aluminum bolts are used for injector hold down bolt torque measurements.
Q: What is the purpose of maintaining Injector Hold Down Bolt Torque? <\N>
A: The purpose of maintaining injector hold down bolt torque is to prevent engine damage, as well as increase the efficiency of the fuel delivery system.
Q: What tools are commonly used for Injector Hold Down Bolt Torque Measurement? <\N>
A: Manual wrenches and digital gauges are typically used for injector hold down bolt torque measurement.
Q: What steps should be followed while tightening the bolt? <\N>
A: When tightening the bolt, it’s important to ensure proper gapping and apply proper pressure using the tool.
Q: What are the benefits of properly tightened injector bolts? <\N>
A: Properly tightened injector bolts offer benefits such as protection for genuine spare parts, better performance, and increased reliability.
In conclusion, the proper torque for 7.3 injector hold down bolts is 18-22 ft-lbs. It is important to remember that this torque should be applied with a torque wrench and the bolts should be tightened in a crisscross pattern. Following these specifications will ensure that the injectors are held securely in place and operating correctly.
Author Profile
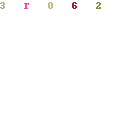
-
Welcome to Liberty Is Viral, a digital nexus where curiosity is the currency and knowledge is the merchandise. We are not just another blog on the block; we are a movement, a collective of inquisitive minds committed to the ethos of liberating information and empowering individuals.
Our journey began with a simple yet profound belief: knowledge should be accessible to all, unrestricted by barriers, free as the air we breathe. Thus, in the bustling digital landscape of 2023, LibertyIsViral.com was reborn, a revitalized platform poised to quench the intellectual thirst of discerning netizens. And we can say we are a bit successful on that, since our community is expanding by the day (20,000 readers and increasing!)
Latest entries
- March 22, 2023AppliancesThe Best 2 Inch Brass Fire Hose Nozzle for Maximum Firefighting Efficiency
- March 22, 2023AppliancesElevate Your Brand with the Best Custom Next Service Due Stickers
- March 22, 2023Lawn, Patio And Exterior5 Best Bird Netting Solutions for Protecting Cherry Trees
- March 22, 2023Apparel And JewelryFind the Best Drop Cut T-Shirt for Men: Our Top Picks