Understanding Electrical Fuel Pump Wires Color Codes: A Comprehensive Guide
The specific color codes of electrical fuel pump wires vary by manufacturer.
Electrical Fuel Pump Wires Color Codes
Electrical fuel pumps require wires to be connected to ensure the proper proper functioning and transfer of fuel. While the specific wiring requirements will vary, depending on the type of pump, there are general color codes that identify which wires should be connected together. Generally, black or red wires are used for power delivery and white or yellow for ground connections. Other colored wires may indicate a warning light or other sensing devices. With proper installation and connection of these color coded wiring harnesses, your fuel pump will continue to provide dependable operation.
Types of Wires
When installing an electric fuel pump, it is important to understand the different types of wires and their color codes. Alternator wires are used to power the fuel pump, while ignition wires are used to turn it on and off. Alternator wires are usually thicker than ignition wires, which can help identify them in a wiring harness. It is also important to note that the color codes used for alternator and ignition wires may vary depending on the make and model of the vehicle.
Color Codes
The color codes for alternator and ignition wires can vary depending on the vehicle model, but generally speaking alternator wires will be red or black in color. Ignition wires will often be yellow or blue in color. It is important to check with your vehicle’s manufacturer to determine which colors are used for alternator and ignition wires in your particular model before beginning installation.
Installation Techniques
When installing an electric fuel pump, it is important to identify the correct connectors for installation as well as follow specific installation methods that may vary by make and model of vehicle. To begin, locate the correct connectors in your wiring harness that will accept both electrical power (from alternator) and ground (from ignition). Once these connections have been identified, you can begin connecting the electrical components of your electric fuel pump system.
It is also important to pay attention to any safety instructions included with your electric fuel pump installation kit as well as any instructions provided by your vehicle’s manufacturer when connecting electrical components. Additionally, be sure to follow all local laws regarding automotive repair when installing an electric fuel pump system in order to ensure proper operation and safety when driving.
Electric Fuel Pumps
Electric fuel pumps are used in a variety of automotive applications ranging from passenger cars to heavy-duty trucks and vehicles that require high performance engines such as racing cars. There are several different types of electric fuel pumps available including mechanical diaphragm pumps, vane pumps, gear pumps, rotary vane pumps, roller vane pumps, swirl chamber pumps and centrifugal pumps – each type having its own application specific benefits. The most common type found in passenger cars today is a mechanical diaphragm pump due its simplicity and low cost of operation compared with other types of electric fuel pumps on the market today.
Testing and Troubleshooting Techniques
Once an electric fuel pump has been successfully installed into a vehicle’s engine bay or trunk area, it is important to test its operation before attempting any further repairs or modifications that may be necessary for proper functioning of the system as a whole. To do this properly first turn off all power sources such as battery switches or circuit breakers before testing any electrical components within your system – this includes testing all wiring connections between components as well as testing each component itself with an ohmmeter or multimeter if necessary.
To test a fuel pump circuit you should use a 12-volt test light connected directly across both terminals within the circuit if one terminal is hot while another is not then there may be a shorted wire somewhere along that circuit which should be located promptly before attempting further repair work on any other component within your system. Common problems with electric fuel pumps include faulty wiring connections due to corrosion over time or incorrect installation procedures – both should be checked immediately if you suspect any problems with your systems performance after installation has been completed successfully.
Safety Precautions – Working on Electrical Systems
Working on any type of electrical system requires safety precautions in order to prevent serious injury or death. Before beginning, it is important to take the necessary steps to ensure the safety of yourself, those around you, and the system itself. This includes understanding the proper use of tools and equipment, being aware of any potential hazards, and taking all necessary safety measures.
When working on an electrical fuel pump, it is important to make sure all power sources are turned off before beginning. It is also important to use the correct tools and equipment for the job at hand. The proper tools will help ensure that the job is done correctly and safely. It is also important to wear protective clothing such as gloves, goggles, and a face mask when working with any type of electrical system.
Materials Needed for Installation
In order to properly install an electric fuel pump, there are specific materials that are needed for the installation process. These materials include terminal connectors and wire strips for connecting the pump to its power source, as well as a power supply for the electric fuel pump itself. Depending on the type of fuel pump being installed, additional materials may be required such as a regulator or pressure switch.
It is important to select materials that are compatible with one another in order to ensure proper performance and reliability from your electric fuel pump. Additionally, it is important to make sure that all connections are properly secured using high quality connectors in order to prevent any accidental disconnection or short circuits during operation.
Benefits of Installing an Electric Fuel Pump
Installing an electric fuel pump has numerous benefits over traditional mechanical pumps including increased efficiency and performance levels as well as improved vehicle safety features. An electric fuel pump eliminates many of the problems associated with mechanical pumps by providing higher levels of reliability and accuracy while reducing maintenance costs due to its self-regulating design which automatically adjusts fuel flow based on engine demand. Additionally, electric pumps can be configured in various ways depending on their application which makes them very versatile in terms of their use in different vehicles or engines.
Alternator To Electric Fuel Pump Connection Resolution
When connecting an alternator to an electric fuel pump it is important to first estimate how much power will be required from your alternator in order for your electric fuel pump system to operate properly without risking damage or compromising performance levels. After estimating your power requirements you can then connect your alternator directly using appropriate connectors such as battery cable terminals or fuse blocks for larger loads. It is also important to make sure that all connections are secure so that nothing becomes loose during operation which could potentially cause damage or create a hazardous situation if left unchecked.
When connecting an alternator directly it is also important not only connect it but also configure its settings accordingly so that it can provide enough power while still protecting your components from any potential overloads or surges caused by sudden changes in demand from your engine or other components connected along with your electric fuel pump system. Proper configuration can be done manually but there are also specialized products available which can simplify this process significantly while ensuring optimal performance levels at all times regardless of load demands placed upon your system.
FAQ & Answers
Q: What are the common wire color codes for an electrical fuel pump?
A: Common wire color codes for an electrical fuel pump include black, brown, red, purple, green, white and yellow.
Q: What does each wire represent for an electrical fuel pump?
A: The black wire is the ground wire and connects to the negative terminal on the battery. The brown wire is the positive power supply from the battery. The red and purple wires are usually connected to the ignition switch. The green wire is for a low-voltage connection to a tachometer or other instrumentation. Finally, the white and yellow wires are used for high-voltage connections to the fuel pump relay.
Q: What should be done when wiring an electrical fuel pump?
A: When wiring an electrical fuel pump, it’s important to use a safe and secure method of wiring. All connections should be soldered and properly insulated with heat shrink tubing or other suitable insulating material. It’s also a good idea to use a dedicated fuse or circuit breaker in order to protect against any possible short circuits or overloads in the wiring circuit.
Q: Is there a way to test if an electrical fuel pump is functioning correctly?
A: Yes, there is a way to test if an electrical fuel pump is functioning correctly. First, check that all of the correct wires are connected in their respective locations according to your vehicle’s wiring diagram. Then turn on your vehicle’s ignition switch with all accessories off and listen for a hum coming from the pump. If you hear this hum then your pump is likely functioning correctly; if not then you may need to replace it or investigate further into potential issues with its connections or associated components in order to get it working again properly.
Q: Are there any safety considerations when dealing with an electrical fuel pump?
A: Yes, it’s very important that safety precautions be taken when dealing with any type of automotive electrical system including those involving fuel pumps. Always make sure that all connections are securely fastened and appropriately insulated before turning on any power source in order to avoid any potential incidents such as fires or electric shock hazards due to exposed bare wires or loose connections during operation of your vehicle’s engine or other components.
In conclusion, the electrical fuel pump wires color codes vary depending on the make and model of your vehicle. Understanding these color codes is essential for anyone working on their vehicles fuel system. By correctly identifying the wires, you can be sure to properly attach them to their respective terminals. Additionally, it’s important to always use the correct gauge of wire when connecting any components in an electrical system.
Author Profile
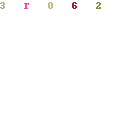
-
Welcome to Liberty Is Viral, a digital nexus where curiosity is the currency and knowledge is the merchandise. We are not just another blog on the block; we are a movement, a collective of inquisitive minds committed to the ethos of liberating information and empowering individuals.
Our journey began with a simple yet profound belief: knowledge should be accessible to all, unrestricted by barriers, free as the air we breathe. Thus, in the bustling digital landscape of 2023, LibertyIsViral.com was reborn, a revitalized platform poised to quench the intellectual thirst of discerning netizens. And we can say we are a bit successful on that, since our community is expanding by the day (20,000 readers and increasing!)
Latest entries
- March 22, 2023AppliancesThe Best 2 Inch Brass Fire Hose Nozzle for Maximum Firefighting Efficiency
- March 22, 2023AppliancesElevate Your Brand with the Best Custom Next Service Due Stickers
- March 22, 2023Lawn, Patio And Exterior5 Best Bird Netting Solutions for Protecting Cherry Trees
- March 22, 2023Apparel And JewelryFind the Best Drop Cut T-Shirt for Men: Our Top Picks