Solve Your Not Pressurizing Eliminator Pump Sprayer Issues Easily
Check for a blockage or obstruction in the hose that could be preventing pressure.
Eliminator Pump Sprayer Not Pressurizing
The Eliminator Pump Sprayer is an ideal tool for helping you evenly apply common garden chemicals while minimizing your exposure to them. Unfortunately, sometimes these tools can stop pressurizing and wont spray properly. If your Eliminator Pump Sprayer is not pressurizing, here is a quick overview of troubleshooting methods to help you get back on track:
1. Check the Pump Mechanism: Look for any physical obstructions such as clogged nozzles, kinks or dents in the hose, or a worn gasket or seal that could be preventing pressurization. Clear any blockage and replace any faulty parts.
2. Determine the Cause of the Blockage: Grit or dirt particles can often get stuck in nozzles and hoses which prevents the pump from pressurizing correctly. Check to see if the airstream covering has been left off while storing the pump which can lead to an accumulation of foreign objects inside. If so, open up the nozzle and clean out anything that shouldnt be inside it.
3. Tighten Nuts and Connectors: Sprayers depend on numerous nuts and connectors to ensure proper pressurization throughout their construction – if any part is too loose it may result in leaking air pressure or even complete lack of pressure. Make sure all areas are securely tightened before operating your pump again.
4. Inspect O-rings and Gaskets: Over time these parts can wear out due to usage or improper storage, so its important to make sure they havent failed prematurely for whatever reason. Replacing OEM O-rings and gaskets immediately should fix any problems with low pressure quickly and easily!
By following these simple steps you should have your Eliminator Pump Sprayer pressurizing correctly soon enough! Enjoy using your well-maintained pump again!
Eliminator Pump Sprayer Not Pressurizing
It’s not uncommon for pump sprayers to not pressurize properly. This can be incredibly frustrating, especially if you need the sprayer for a specific task. Fortunately, there are a few steps you can take to diagnose and troubleshoot your pump sprayer.
Check Valve Mechanism
The first step is to check the valve mechanism. This involves examining the valve mechanism itself, as well as the rubber seals that are located in the valve assembly. If any of these components are damaged or worn out, it can lead to air leaks and prevent proper pressurization. You’ll want to replace any damaged parts before continuing with your troubleshooting process.
Troubleshooting Steps
Once you’ve identified and replaced any faulty components, you should then begin your troubleshooting process. This includes checking for blockages in the hose or nozzle assembly, as well as inspecting all connections for air leaks. If everything looks okay on this front, then it might be time to check the pump’s pressure gauge and adjust it accordingly. You should also ensure that the pump is properly lubricated and has enough oil in it to operate properly.
Regulating Pressure Output for Pump Sprayers
If your pump sprayer is still not pressurizing correctly after all of these steps, then it might be time to look into regulating its pressure output. This involves adjusting the regulator knob on the pump until you get an acceptable pressure level. It’s important to note that each sprayer type has its own optimal pressure range, so make sure you know what this range is before making any adjustments. Once you have adjusted the regulator knob, test it out by spraying a small amount of water onto a surface and see how it responds – if it’s still not working correctly then try adjusting again until you get an acceptable result.
Replacing The Hose Connector
In some cases, replacing the hose connector might be necessary if you’re having issues with your eliminator pump sprayer not pressurizing correctly. The hose connector is responsible for connecting the hose to the nozzle assembly and ensuring that there is a secure connection in place between them so that no air leakage occurs during operation. If this connection isn’t made correctly or if there are any damages present on either end of the connector then this could lead to issues with pressurization so it’s important that they are replaced immediately if necessary.
Replacing The Nozzle Filter
The nozzle filter on an eliminator pump sprayer is responsible for preventing debris from entering into your spray stream which could cause problems with pressurization and clogging of nozzles over time. If your nozzle filter has become clogged or damaged due to wear-and-tear then replacing it may be necessary in order to ensure proper operation of your eliminator pump sprayer once again – simply unscrewing and replacing with a new one should suffice here!
Preventative Maintenance On Eliminator Pump Sprayers
Preventative maintenance on an eliminator pump sprayer is incredibly important if you want it to work properly over time without any issues arising from poor maintenance practices over long periods of use! This involves regularly inspecting all components of the system including hoses, nozzles, filters etc., cleaning them when necessary (this can include using specific cleaning solutions depending on what materials they’re made from) as well as lubricating all moving parts where needed in order keep things running optimally at all times!
Cleaning And Storing Your Eliminator Pump Sprayer
When storing your eliminator pump sprayer after use (or even when putting away after completing maintenance tasks) its best practice to fully dismantle each component separately and clean each part thoroughly before reassembling – this ensures maximum longevity of all parts involved as well as reducing potential damage caused by built up debris over long periods of time! Additionally sanitizing all parts prior to reassembly will also help ensure they remain free from bacteria or other contaminants which could potentially harm people or objects when used later down the line!
Choosing the Right Nozzle Tip for Your Sprayer
When it comes to getting the most out of your Eliminator Pump Sprayer, selecting the right nozzle tip and ensuring a balanced pressure setting is essential. Selecting a nozzle opening size that is too small can result in weak spray patterns and low pressure, while an opening size that is too large can lead to high pressure and reduced performance. To ensure optimal performance and proper pressure settings, its important to select a nozzle opening size that is right for your application.
When selecting a nozzle opening size, consider the type of material youll be spraying, the distance between the sprayer and the target surface, and how much coverage you need. For example, if youre spraying a fine material such as paint or stain from close range (less than 10 feet away), then youll want to select a smaller nozzle opening size. If youre spraying thicker materials such as sealants or adhesives from farther away (more than 10 feet away), then you should select a larger nozzle opening size.
Its also important to ensure that your pressure settings are balanced in order to maximize performance and minimize wear on the pump components. Too much pressure can damage your pump while too little pressure can lead to weak spray patterns and reduced coverage. The ideal balance should be established after testing both at idle speed (with no load) and under full load (when spraying). This will help ensure that your Eliminator Pump Sprayer operates correctly and efficiently every time.
Enhancing Water Flow From Your Eliminator Pump Sprayer
Getting optimal water flow out of an Eliminator Pump Sprayer requires some modifications beyond what comes standard with most models. There are several common modifications that can be done to increase water flow rate and overall performance from your Eliminator Pump Sprayer. These include: increasing pump speed with larger pulleys, replacing worn-out nozzles with higher-flow ones, installing larger shutoff valves for more efficient water delivery, adding bypass lines for better circulation when running multiple nozzles simultaneously, upgrading hose connections with quick-connect fittings for faster setup time, installing filters in-line to reduce clogging or corrosion damage, or replacing worn parts such as seals or O-rings with higher quality ones.
Maximizing efficiency through upgrades is key when it comes to getting better performance out of an Eliminator Pump Sprayer. Its important to remember that these upgrades should be done according to best practices laid out by the manufacturer in order to maintain warranty coverage on your machine. Additionally, if any changes are made outside of manufacturer specifications then it may be necessary to adjust other settings accordingly in order for everything to work properly together.
Removing Excess Air From The Tank On An Eliminator Pump Sprayer
Air bubbles in tanks on Eliminator Pump Sprayers can cause reduced performance due to decreased air volume which reduces water flow rate out of the nozzles. To avoid this issue it’s important to purge any air bubbles from the tank before use by turning on both pumps simultaneously while slowly increasing water flow rate until all air bubbles have been removed from both pumps’ suction lines. It’s also helpful to check all connections along both suction lines prior to starting up each time as small leaks due improper sealing or worn gaskets can cause air bubbles which will reduce performance when spraying liquids or thick materials like paints or adhesives.
Diagnosing Malfunction in Your Eliminator Pump Sprayer
When diagnosing malfunction in an Eliminator Pump Sprayer there are several signs that should be looked out for which may indicate an underlying problem with one or more components of the machine such as insufficient water flow rate due clogged filters; excessive noise from either pump indicating worn parts; leaks along hose connections indicating faulty O-rings; insufficient cooling due blocked fan openings; lack of sealant due worn seals; inadequate lubrication causing friction between moving parts; abnormally high temperatures indicating electrical malfunctions; or unusual vibrations caused by misaligned components resulting in premature wear and tear on certain parts of the machine over time leading eventually leading up premature failure if left unchecked. As such it’s important not only anticipate potential problems but also take proactive steps towards addressing them before they become major issues affecting long term operation of your machine over time
FAQ & Answers
Q: How do I know if the check valve mechanism on my Eliminator Pump Sprayer is working?
A: To check if the check valve mechanism is functioning properly, you can test it by disconnecting the hose from the sprayer and then turning it on. If the pump pressurizes, then the check valve is working correctly. If not, it may need to be replaced or repaired.
Q: What are some potential issues that could cause my pump sprayer to not regulate its pressure output correctly?
A: Potential issues that could prevent proper pressure regulation include a blocked nozzle filter, an incorrectly sized nozzle tip, or a damaged hose connector. Additionally, excess air in the tank can also cause pressure regulation issues.
Q: What should I do when replacing the hose connector on my Eliminator Pump Sprayer?
A: When replacing the hose connector on your Eliminator Pump Sprayer, make sure to use a compatible connector that fits tightly and securely onto both ends of the hose. It’s also important to ensure that all connections are properly tightened with pliers before use.
Q: How should I store my pump sprayer after use?
A: After use, it’s important to clean and store your Eliminator Pump Sprayer properly in order to maintain its quality and extend its life span. This includes dismantling and reassembling all parts before sanitizing them with soap and water. For further protection from damage, you can also add a layer of lubricant onto any metal components.
Q: How do I maximize water flow from my Eliminator Pump Sprayer?
A: To maximize water flow from your Eliminator Pump Sprayer, you can consider making modifications such as changing out your nozzle tip for one of a larger opening size or installing an additional bypass valve in order to provide additional pressure relief for better flow control. Additionally, removing any excess air in the tank can also help improve water flow performance.
The most common cause of an Eliminator pump sprayer not pressurizing is a clogged or blocked filter. If the filter is clear, check the pressure relief valve and the diaphragm for any damage or wear. If these components are functioning correctly, replace the piston/plunger assembly and check for a broken spring or seal. If all of these components are functioning correctly, then it may be necessary to replace the entire sprayer unit.
Author Profile
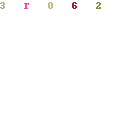
-
Welcome to Liberty Is Viral, a digital nexus where curiosity is the currency and knowledge is the merchandise. We are not just another blog on the block; we are a movement, a collective of inquisitive minds committed to the ethos of liberating information and empowering individuals.
Our journey began with a simple yet profound belief: knowledge should be accessible to all, unrestricted by barriers, free as the air we breathe. Thus, in the bustling digital landscape of 2023, LibertyIsViral.com was reborn, a revitalized platform poised to quench the intellectual thirst of discerning netizens. And we can say we are a bit successful on that, since our community is expanding by the day (20,000 readers and increasing!)
Latest entries
- March 22, 2023AppliancesThe Best 2 Inch Brass Fire Hose Nozzle for Maximum Firefighting Efficiency
- March 22, 2023AppliancesElevate Your Brand with the Best Custom Next Service Due Stickers
- March 22, 2023Lawn, Patio And Exterior5 Best Bird Netting Solutions for Protecting Cherry Trees
- March 22, 2023Apparel And JewelryFind the Best Drop Cut T-Shirt for Men: Our Top Picks