What is Engine Derate In 3 Hours and Why It Is Important?
Engine derate in 3 hours meaning that the engine will reduce its power output after 3 hours of operation.
Engine Derate In 3 Hours Meaning
Engine Derate In 3 Hours Meaning is a term used to indicate the reduction in engine power output over a period of three hours. It essentially occurs when an aircraft engine is operating more heavily than its manufacturer recommends, often leading to reduced thrust and slower climb rates. This practice is far from ideal and can cause serious issues for aircraft if done incorrectly or carelessly. The derate can be caused by overheating, too much exhaust gas temperature, or an unexpected increased air/gas flow imbalance. The surest way to prevent this from happening is by sticking to the recommended takeoff power given by the manufacturer and ensuring that the aircraft is properly running at full capacity – with any potential faults identified and corrected before flight.
Engine Derate In 3 Hours Meaning
Engine derate in 3 hours is an emergency procedure that requires an aircraft to reduce the power of its engines in order to prevent the engine from over-heating and possibly damaging the aircraft. This procedure is typically used to protect the engine from further damage and to ensure the safety of passengers and crew. The procedure must be followed precisely as outlined by a manufacturer and should not be attempted without proper training and guidance.
Causes of Engine Derate In 3 Hours
There are several potential causes of engine derate in 3 hours, with heat related issues being one of the most common culprits. Heat can build up quickly inside an engine compartment due to a variety of factors, such as improper airflow or inadequate cooling components, which can lead to excessive temperatures which could cause damage or even catastrophic failure. Fuel system problems can also be a cause, with air or fuel lines becoming blocked or restricted, causing a decrease in power output.
Specifications For Operators
In order for pilots and other operators to understand how to correctly perform a derate procedure in 3 hours, they must first familiarize themselves with the specific aircraft/engine model detail that applies to their particular situation. This includes information on power levels that must be maintained during various stages of flight as well as maintenance intervals for inspections, part replacements, and other necessary processes.
Prevention Of Engine Derate In 3 Hours
The best way to prevent an engine derate situation is through regular maintenance checkups and proper servicing of all relevant components. One important task is tray cleaning and greasing which helps ensure that all parts are properly lubricated and functioning correctly. Additionally, it’s important for operators to keep detailed logs of all checks and maintenance procedures performed so that any issues can be identified quickly before they result in a derate situation.
Implications Of Unchecked Engine Derate In 3 Hours
If an engine derate situation is not addressed promptly it can result in high EGT (exhaust gas temperature) levels which can significantly decrease the lifespan of the engine. Additionally, if left unchecked it could also lead to increased risk of explosion or fire hazards due to extreme temperatures within the engine compartment. It’s therefore essential that operators take all necessary steps when performing a derate procedure in order to protect their aircraft from damaging effects or potential fire hazards.
Engine Derate In 3 Hours Meaning
Engine derating describes the process of decreasing the power output of an engine due to performance issues or safety concerns. This is done in order to prevent potential damage or further issues that could arise from running the engine at its full power. The phrase engine derate in 3 hours is used to describe a particular type of engine derating that occurs after the engine has run for three hours without any issues.
Limitations of Conventional Sensor Technologies
Conventional sensors are limited in their ability to detect and report on the performance of an engine. This can lead to incorrect readings and inaccurate data being reported, which can then potentially lead to mechanical failures or other issues. Additionally, conventional sensors can only be used in relatively stable environmental conditions, as they cannot handle extreme temperatures or pressure changes. As such, they are not suitable for monitoring engines in harsh conditions, such as those found on aircrafts or high-performance vehicles that require precise readings at all times.
Benefits of Advanced Technology For Monitoring Engine Performance
Advanced technology offers a number of benefits when it comes to monitoring an engines performance. For starters, these technologies provide real-time data and can detect even small variations in performance before they become a major issue. Furthermore, these technologies come with automation capabilities that can allow operators to act quickly on any detected problems before they become serious and cause costly repairs or downtime. Finally, advanced technology also allows for predictive maintenance, which means operators can identify potential problems before they occur and take preventative measures accordingly.
Possible Solutions To Overcome Limitations Of Traditional Monitoring System
There are several solutions available for overcoming the limitations of traditional monitoring systems when it comes to engines. One solution is to improve sensor reliability and accuracy with advanced technologies such as digital signal processing (DSP) algorithms and artificial intelligence (AI). Additionally, automated monitoring systems can be implemented that alert operators when certain thresholds are exceeded which could indicate a potential issue with the engines performance. Finally, remote diagnostics systems can be used which allow technicians access remotely into an engines control system so they can identify and diagnose any problems more quickly and accurately than would be possible with traditional methods.
Cost Effectiveness & Reliability Of Advanced Technologies For Monitoring Engines
The cost effectiveness and reliability of advanced technologies for monitoring engines depend largely on how well these technologies are implemented by the operator or technician responsible for them. If done correctly, advanced technologies offer significant cost savings over time due to improved accuracy and reduced downtime caused by mechanical failures or other issues related to poor performance monitoring. Additionally, uptime improvements through preemptive maintenance enabled by these advanced technologies mean fewer unexpected breakdowns during operation which also leads to cost savings over time.
FAQs & Answers
Q: What is Engine Derate?
A: Engine derate is a term used to describe the reduction of an engine’s power output when it reaches certain limits for a prolonged period of time. This can be caused by heat-related issues, fuel system problems, or other factors.
Q: What are the guiding principles of engine derate?
A: The guiding principle of engine derate is to ensure the safe and reliable operation of aircraft engines. This includes restrictions on maximum speeds, temperatures, and other parameters that must be maintained for safe operation.
Q: What are the specifications for operators when dealing with engine derate in 3 hours?
A: When dealing with engine derate in 3 hours, operators must have detailed information about their aircraft and engine model. They should also be aware of maintenance intervals for inspections as this will help reduce the risk of engine derate.
Q: How can I prevent engine derate in 3 hours?
A: To prevent engine derate in 3 hours, operators should regularly check and clean trays as well as keep detailed maintenance logs. This will reduce the risk of heat-related issues and ensure that any problems are detected before they cause permanent damage to the engine.
Q: What are the implications of unchecked engine derate in 3 hours?
A: If left unchecked, high EGT levels can lead to decreased lifespan of an aircraft’s engines and may increase the risk of explosion or fire hazards. Therefore, it is important to monitor engines regularly and take steps to prevent any potential issues before they become a problem.
Engine derate in 3 hours meaning is that an aircraft engine will reduce its power output by a certain percentage after it has operated continuously for three hours. This is done to prevent the engine from being damaged due to excessive heat or wear and tear. Engine derate helps to ensure the safe operation of an aircraft and its passengers, and it is important for pilots to understand how to recognize and respond to this situation.
Author Profile
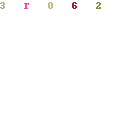
-
Welcome to Liberty Is Viral, a digital nexus where curiosity is the currency and knowledge is the merchandise. We are not just another blog on the block; we are a movement, a collective of inquisitive minds committed to the ethos of liberating information and empowering individuals.
Our journey began with a simple yet profound belief: knowledge should be accessible to all, unrestricted by barriers, free as the air we breathe. Thus, in the bustling digital landscape of 2023, LibertyIsViral.com was reborn, a revitalized platform poised to quench the intellectual thirst of discerning netizens. And we can say we are a bit successful on that, since our community is expanding by the day (20,000 readers and increasing!)
Latest entries
- March 22, 2023AppliancesThe Best 2 Inch Brass Fire Hose Nozzle for Maximum Firefighting Efficiency
- March 22, 2023AppliancesElevate Your Brand with the Best Custom Next Service Due Stickers
- March 22, 2023Lawn, Patio And Exterior5 Best Bird Netting Solutions for Protecting Cherry Trees
- March 22, 2023Apparel And JewelryFind the Best Drop Cut T-Shirt for Men: Our Top Picks