Understanding the Role of Hydraulic Lifters in Keeping Valves Open
Hydraulic lifters are used to keep valves open while the engine is running.
Hydraulic Lifters Holding Valves Open
Hydraulic lifters are devices used to open and close valves. They are able to precisely apply just the right amount of pressure needed in order to operate the valve. This makes them very useful in many industries, from automotive to engineering. The hydraulic lifter is an efficient, reliable way of keeping valves open as and when required. It consists of two parts – a rod and an actuator. The actuator controls the rod which moves, allowing the valve to open or close. The hydraulic lifter holds the valves open by using pressure from oil or hydraulics which is sent through the lifters rod and turns the valve in turn. This action holds open valves securely and accurately, allowing for precise control over the opening of valves for exact periods of time depending on what is desired. By using hydraulic lifters to keep valves open, businesses can save both time and money while ensuring safety and accuracy.
Different Types Of Hydraulic Lifters
Hydraulic lifters are an essential component in any car engine. They are used to keep the valves open during operation, allowing for the fuel to be burned and the exhaust gases to be expelled. The two main types of hydraulic lifters are the roller hydraulic lifter and the solid or flat tappet hydraulic lifter.
The roller hydraulic lifter consists of a plunger which is pushed down by a camshaft lobe, forcing oil through a small valve at the bottom of the plunger. This oil pressure then forces a roller which is connected to the plunger, to rotate against a cam shaft lobe, causing it to push down on the valve stem keeping it open during engine operation.
The second type of hydraulic lifter is known as a solid or flat tappet hydraulic lifter. This type of lifter uses an internal spring that is pushed down by a camshaft lobe, forcing oil through an inlet hole in the top of the plunger. This oil pressure then pushes down on a flat tappet at the bottom of plunger, keeping it engaged with the camshaft lobe and keeping the valve open during engine operation.
How Hydraulic Lifters Work
Hydraulic lifters work by using pressurized oil to engage and disengage locks which keep valves open during engine operation. When oil pressure is applied through small valves at either end of each plunger, it forces pushrods to move up and down, effectively activating both intake and exhaust valves at their designated times. The pressurized oil also allows for clearance between moving parts within each individual cylinder head as well as between different cylinders in an engine block, preventing unnecessary wear on these components over time.
Benefits Of Hydraulic Lifters
Using hydraulic lifters has several benefits which include reduced maintenance requirements and improved performance from an engine due to improved valve timing accuracy and longer-lasting components within each cylinder head due to reduced friction from pressurized oil being used instead of mechanical locks or springs. This also allows for easier adjustments when tuning an engine as well as ensuring consistent performance with fewer required repairs over time.
Factors To Consider When Installing A Hydraulic Lifter
When installing hydraulic lifters into any vehicles engine, there are several important factors that must be taken into consideration in order to ensure proper performance from your vehicles motor over time. These factors include compatibility with your vehicles engine configuration, such as its bore size or stroke length; choosing between either roller or solid/flat tappet lifters; and ensuring that all components are correctly installed before starting your vehicles motor for its first time after installation. Additionally, you should always use high-quality oils when installing new hydraulic lift systems as this will help reduce wear on internal components over time and improve overall performance from your vehicles motor for years to come.
Common Problems With Hydraulic Lifters
While there are several benefits associated with using hydraulic lift systems in vehicles today, there can also be some common problems associated with them if they are not properly maintained or installed correctly into vehicles engines initially. Common problems that can arise include issues with an inadequate supply of pressurized oil due to either worn-out pumps or faulty filters; issues with unstable valve timing due to incorrect adjustment; and excessive noise coming from within each individual cylinder head due to loose parts or inadequate lubrication between moving components within each cylinder head assembly itself. To prevent these issues from arising it is important that all components of your vehicle’s motor are inspected regularly by qualified mechanics in order for them to identify any potential problems before they become too difficult (or expensive!) To repair later on down the line!
Diagnosing Malfunctioned Hydraulic Lifters
Troubleshooting the causes of malfunctioned hydraulic lifters is essential for keeping your engine running in top condition. The first step to diagnosing a malfunctioning hydraulic lifter is to analyze the symptoms. Common symptoms of a malfunctioning hydraulic lifter include an engine noise, such as knocking or ticking, that increases or decreases with engine speed, as well as an increase in oil pressure. If these symptoms are present, it is important to identify the source of the problem before attempting any repairs.
Once the source of the problem has been identified, it is important to determine if the cause is a faulty part or if there is an issue with the hydraulic lifter itself. To do this, it may be necessary to disassemble and inspect all components involved in order to determine if any parts need to be replaced. If a faulty part is found, it should be replaced and reassembled properly in order to ensure proper operation of the system.
Preventative Measures For Healthy Hydraulic Lifters
Maintaining healthy hydraulic lifters involves monitoring oil levels and replacing worn parts regularly. It is important to check your oil levels regularly and replace any worn parts immediately in order to prevent further damage or malfunctions down the line. Additionally, it is important to ensure that all components are properly lubricated and securely tightened in order for them to function correctly.
Another preventative measure that should be taken when dealing with hydraulic lifters involves keeping them clean and free from debris or dirt buildup. Dirt can accumulate on certain areas of a hydraulic lifter over time which can lead to clogging and reduced efficiency of its operation. This should be avoided by regularly cleaning and inspecting each component of the system for signs of dirt or debris buildup before reassembly occurs.
Potential Consequences Of Failing To Monitor Valves Inplace With Hydraulic Lifters
Failing to monitor valves in place with hydraulic lifters can have serious consequences on engine performance if not addressed promptly. Some potential consequences include poor performance from the engine due excessive wear on parts, overheating of the engine from increased friction caused by improper valve timing, as well as damage beyond repair to other components due to extended wear or improper lubrication. In some cases, this could even lead to complete engine failure if left unattended for too long.
It is therefore very important that regular maintenance checks are performed on valves in place with hydraulic lifters so that any issues can be identified quickly and remedied before they become more serious problems down the line. This will help keep your engine running smoothly and reduce wear on other parts over time which could otherwise become damaged beyond repair over time if left unchecked for too long periods of time due lack of proper maintenance tasks being performed regularly throughout its lifespan.
Tips For Troubleshooting Malfunctioned/Leaky Valve-Lift System
Troubleshooting a malfunctioned/leaky valve-lift system requires identifying what part may be causing an issue as well as repairing or replacing any affected parts accordingly so that they function properly once again. The first step when troubleshooting this type system would involve locating any signs of leaks or malfunctions within each component within its system such as seals which may have been cracked or worn out over time due lack of proper maintenance checks being performed regularly throughout its lifespan thus far; Once identified then it would be important then replace these affected seals immediately so that they are able maintain their effectiveness once again when reassembling them back into their respective location within its system afterwards thus restoring full functionality back into its operating state once again afterwards thus allowing you restore your vehicle back into top operating condition once again afterwards at end result afterwards all without needing professional help!
FAQ & Answers
Q: What are hydraulic lifters?
A: Hydraulic lifters are components of an internal combustion engine that transfer the force of the camshaft to the valves, allowing them to open and close as needed. They use oil pressure to engage a lock and pushrods which in turn activate the valves.
Q: What are the different types of hydraulic lifters?
A: There are two main types of hydraulic lifters – roller hydraulic lifter and solid or flat tappet hydraulic lifter. Roller hydraulic lifters have a roller bearing between the plunger and cam lobe, while solid or flat tappet hydraulic lifters have a flat tappet surface instead.
Q: What are the benefits of using hydraulic lifters?
A: Hydraulic lifters provide improved performance for an engine and require less maintenance than other types of valve-lift systems. Additionally, they tend to be more durable and reliable over time.
Q: What factors should be considered when installing a hydraulic lifter?
A: It is important to ensure that the type of hydraulic lifter being installed is compatible with your engine configuration. Additionally, you should consider what type of lift you need for your specific application.
Q: Are there any common problems associated with hydraulic lifters?
A: Common problems associated with hydraulic lifters include oil pump problems, unstable valve timing, and excessive wear on parts due to lack of proper maintenance. It is important to regularly monitor your oil levels and replace worn parts in order to prevent any issues from arising with your valve-lift system.
In conclusion, hydraulic lifters are a critical component of engine operation, as they are responsible for holding valves open during the combustion process and allowing fuel and air to enter the combustion chamber. If a lifter fails, it can lead to decreased engine performance and even damage to other components. Proper maintenance is key for keeping hydraulic lifters functioning properly and ensuring optimal engine performance.
Author Profile
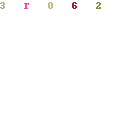
-
Welcome to Liberty Is Viral, a digital nexus where curiosity is the currency and knowledge is the merchandise. We are not just another blog on the block; we are a movement, a collective of inquisitive minds committed to the ethos of liberating information and empowering individuals.
Our journey began with a simple yet profound belief: knowledge should be accessible to all, unrestricted by barriers, free as the air we breathe. Thus, in the bustling digital landscape of 2023, LibertyIsViral.com was reborn, a revitalized platform poised to quench the intellectual thirst of discerning netizens. And we can say we are a bit successful on that, since our community is expanding by the day (20,000 readers and increasing!)
Latest entries
- March 22, 2023AppliancesThe Best 2 Inch Brass Fire Hose Nozzle for Maximum Firefighting Efficiency
- March 22, 2023AppliancesElevate Your Brand with the Best Custom Next Service Due Stickers
- March 22, 2023Lawn, Patio And Exterior5 Best Bird Netting Solutions for Protecting Cherry Trees
- March 22, 2023Apparel And JewelryFind the Best Drop Cut T-Shirt for Men: Our Top Picks