Troubleshooting a Secondary Air Tank That Won’t Build Pressure
The secondary air tank is not able to build and maintain enough pressure.
Secondary Air Tank Won’T Build Pressure
A secondary air tank is an important component in the flow of compressed air from an air compressor to its power-using tools. When it won’t build pressure, there are several steps to follow to troubleshoot the problem. First, check the filter and intake valve for any blockages. If these two components haven’t been maintained, then cleaning them is essential for proper functioning. Next, inspect the relief valve and volume control regulator for any damage or malfunction that might be hindering the pressure from building within the tank. Finally, ensure that all connection hoses are properly connected with no loose fittings or leakages. If these steps fail to restore pressure to the tank, further investigation may be needed as there may be another source of the problem.
Secondary Air Pressure
A secondary air pressure tank is an important component of many air systems in industrial and commercial settings. It helps to regulate the pressure and flow of air to equipment and other components, ensuring that they operate safely and efficiently. When the tank is not building pressure, it can lead to problems with these components and create safety hazards. To troubleshoot this issue, it is important to understand the symptoms of low pressure, the possible causes of low pressure, as well as how to clean, replace, and refit the air pump. In addition, checking safety features such as valves and residual pressure valves is also essential.
Symptoms of Low Pressure
The most common symptom of low pressure in a secondary air tank is that equipment powered by compressed air will not operate correctly or produce desired results. Also, if there is a significant decrease in power or output from the equipment despite no other changes being made, this could indicate low pressure in the tank. Low pressure can also be identified by listening for hissing or whistling noises from the tank’s valves or gauges. If these sounds are heard, it could mean that too much air is escaping from the system due to low pressure levels.
Causes of Low Pressure
Low pressure in a secondary air tank can be caused by several factors. One possibility is a faulty compressor that isn’t able to produce enough compressed air to fill up the tank to its desired capacity. Alternatively, if there are any leaks in pipes connected to the system or valves that aren’t opening properly because of debris build-up or damage, then this can also cause problems with maintaining sufficient levels of compressed air in the system. Finally, if too much air is being used at once by multiple components connected to the same tank then this can also cause an overall decrease in available pressure for all components connected to it.
Troubleshooting the Air Tank
To troubleshoot an issue with a secondary air tank not building sufficient levels of pressure, one must first inspect all components associated with it for any signs of damage or debris build-up which could be causing leaks or blocking necessary airflow. This includes checking any hoses connected to it as well as all valves which should be open so that there are no restrictions on airflow into or out of the system. Secondly, if any parts have been damaged then they should be replaced immediately so as not to further impede performance levels.
Refitting The Air Pump
After cleaning and replacing any necessary parts associated with the secondary air tank system then one must refit their pump back into place correctly so that it can start building up proper levels of compressed air again within its associated tanks. This involves making sure all wiring connections are secure as well as setting appropriate pressures within each individual component according to manufacturer recommendations for optimal performance levels when running multiple pieces at once off one system simultaneously.
Troubleshooting Supply Valves
It is important when troubleshooting a secondary air tank system not building sufficient levels of pressure that one ensures all supply valves are open so that adequate amounts of compressed gas are entering into each component from its respective source pipe line(s). To do this efficiently one must inspect supply pipes for any blockages due to debris build-up which could restrict airflow and thus reduce available pressures within each component individually; alternatively these pipes may have developed small cracks over time which can cause leaks meaning too much gas escapes before reaching its intended destination(s).
Checking Safety Features
Finally when troubleshooting an issue with a secondary air tank not building sufficient levels of pressure one must check all relevant safety features associated with each individual piece such as residual valve check valves etc., ensuring they are functioning correctly so as not allow excessive amounts gas enter into any given piece; similarly shut off valves should also be inspected regularly for reliability purposes so that they shut down equipment automatically when required (e.g., when pressures become too high).
Replacing Parts and Connectors
When a secondary air tank won’t build pressure, the first step is to identify faulty fittings and connectors. This may involve examining the tank and its components for signs of wear and tear, corrosion, or other damage. Once any faulty parts have been identified and replaced, it is important to install new components and seals. This will ensure that the pressure in the tank remains consistent and that no further damage is caused by leaking air or fuel.
Maintenance and Refurbishment
In order to maintain a healthy secondary air tank, regular servicing of hoses and clamps should be carried out. This involves testing compressed gas outputs to ensure there are no blockages or leaks, as well as cleaning setters and accumulator tanks to prevent build up of debris. Regular maintenance will help to improve efficiency of the system, prevent further damage from occurring, and ensure that all parts are in good working order.
Methods of Improving Performance Efficiency
When attempting to improve performance efficiency of a secondary air tank, it is important to ensure correct part alignment. This can be done by adjusting existing engine parameters such as cam timing or fuel injection settings. Additionally, changes can be made to regulatory limits such as maximum combustion pressures in order to increase power output without risking damaging components in the process.
Adjustment to Workings Systems
Finally, when attempting to solve issues with a secondary air tank it may be necessary make adjustments to existing workings systems. This could involve making changes to regulatory limits in order to meet safety standards or accounting for adaptive controls which will enable the system to respond dynamically when certain conditions are present. By accounting for these factors when solving problems with a secondary air tank, it is possible to reduce downtime while ensuring that all parts are functioning correctly.
FAQ & Answers
Q: What are the symptoms of low pressure in a secondary air tank?
A: Common symptoms of low pressure in a secondary air tank include difficulty starting the engine, decreased performance, and reduced fuel economy. Additionally, there may be audible signs such as strange noises coming from the air tank or engine.
Q: What are some causes of low pressure in a secondary air tank?
A: Low pressure in a secondary air tank can be caused by a worn or damaged air pump, blocked supply valves, damaged fittings and connectors, or faulty safety features. Additionally, problems with the accumulator tanks or hoses can result in reduced pressure.
Q: How do you troubleshoot an air tank with low pressure?
A: Troubleshooting an air tank with low pressure involves inspecting the components for damage and cleaning the parts that have become blocked or clogged. It is also important to check wiring connections, test residual pressure valves and shut-off valves for reliability, and adjust the pressure levels as necessary.
Q: What methods can be used to improve performance efficiency?
A: Improving performance efficiency involves ensuring correct part alignment and working with existing engine parameters. Additionally, making changes to regulatory limits and accounting for adaptive controls can help maximize performance efficiency.
Q: How do you adjust workings systems for better performance?
A: Adjusting workings systems for better performance requires identifying faulty fittings and connectors then installing new components and seals. Additionally, servicing hoses and clamps as well as testing compressed gas outputs can help ensure optimal performance.
Based on the information available, it appears that the secondary air tank is not building pressure due to a malfunction or blockage in the system. It is likely that further investigation is needed in order to determine the exact cause of the problem. Depending on the issue, a qualified technician may need to be consulted in order to repair or replace any faulty components.
Author Profile
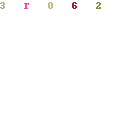
-
Welcome to Liberty Is Viral, a digital nexus where curiosity is the currency and knowledge is the merchandise. We are not just another blog on the block; we are a movement, a collective of inquisitive minds committed to the ethos of liberating information and empowering individuals.
Our journey began with a simple yet profound belief: knowledge should be accessible to all, unrestricted by barriers, free as the air we breathe. Thus, in the bustling digital landscape of 2023, LibertyIsViral.com was reborn, a revitalized platform poised to quench the intellectual thirst of discerning netizens. And we can say we are a bit successful on that, since our community is expanding by the day (20,000 readers and increasing!)
Latest entries
- March 22, 2023AppliancesThe Best 2 Inch Brass Fire Hose Nozzle for Maximum Firefighting Efficiency
- March 22, 2023AppliancesElevate Your Brand with the Best Custom Next Service Due Stickers
- March 22, 2023Lawn, Patio And Exterior5 Best Bird Netting Solutions for Protecting Cherry Trees
- March 22, 2023Apparel And JewelryFind the Best Drop Cut T-Shirt for Men: Our Top Picks