Understanding Torque Specs for Caliper Bolts: A Comprehensive Guide
The required torque for caliper bolts is usually between 18 to 22 Nm (Newton-meters).
Torque Specs for Caliper Bolts
The torque specs for caliper bolts play a critical role in ensuring that your brake calipers are securely mounted and operating correctly. These fasteners, when tightened correctly, ensure the optimal performance of your braking system. The torque specifications for your brake calipers depend on the type of vehicle, as well as the type of bolts used. A wide range of torque values may be referenced depending on these factors. When implementing these torques, it is important to use a reputable torque wrench to accurately measure the tightening process and verify that all bolts are adequately fastened. Following manufacturer recommendations can help protect your safety by ensuring that your brakes remain in top condition.
Caliper Bolt Torque Specs -General Guidelines -Required Tools
When working on a vehicle, it is important to torque the caliper bolts correctly. Properly torquing the bolts will ensure a secure and safe connection between the caliper and the rotor, as well as prevent possible damage or wear to the brake system. To assist in properly torquing these bolts, there are some general guidelines and tools that should be followed.
The first step is to determine what type of bolt is being used for the application. This can typically be found in the vehicles owners manual or in aftermarket databases. Knowing what type of bolt is being used will help to determine which torque specifications are applicable for that particular vehicle model. It is also important to understand what surface type is being worked on during installation. Metal surfaces require dry threads while lubricated threads are needed for plastic surfaces.
In order to properly torque a caliper bolt, it is important to have the correct tools available for the job. A torque wrench should be used for precise measurements in order to achieve proper clamping force and avoid over-tightening or under-tightening of the caliper bolts. Additionally, a ratchet, socket set, and extension are necessary tools when working with caliper bolts.
Understanding Caliper Bolts -Types of Caliper Bolts -Benefits of Torqueing Properly
Caliper bolts come in various sizes and forms depending on their usage and application within a given vehicle model year and manufacturer. There are two main types of caliper boltsstuds and nutsand each has their own purpose when it comes to securing brakes components together securely. Studs are typically used for inner brake components such as rotors while nuts are exclusively used for outer components such as calipers or mounting brackets.
When properly torqued according to manufacturer specifications, these bolts ensure that all brakes components remain secure without any unexpected movement or vibration coming from them during usagethis helps reduce wear on other brakes parts due to improper clamping force which could lead to costly repair bills down the road if not addressed properly ahead of time. Additionally, proper torqueing ensures that all parts remain secure even when under extreme pressure during heavy braking maneuvers ensuring optimal performance from your vehicles braking system at all times.
Assessing The Vehicle Model Year And Manufacturer -Using VIN Number To Determine Model Year -Searching For Specific Manufacturer Bolt Torque Specs
In order to determine which applicable torque specs should be followed when working with caliper bolts on a particular vehicle model year and manufacturer, it is important to assess both factors before beginning work on any brakes component installation job. The first step would be determining the vehicle model year by using its VIN numberthis can typically be found on registration documents or through a variety of online services offered by auto manufacturers across different makes and models so make sure you do your research beforehand if you dont already have this information readily available at hand!
Once this information has been acquired, its time to search for specific manufacturer bolt torque specs pertaining to that particular make/model combinationthis can be done through aftermarket databases or even through ADA compliance databases depending on where you lookonce again make sure you do your research ahead of time so you dont run into any issues down the road!
Working On Different Surface Types During Installation Drives -Metal Surfaces- Dry Threads- Lubricated Threads
When working with different surface types during installation drives it is important that specific steps are taken in order to ensure proper torquing specs are achieved throughout each taskmetal surfaces require dry threads while lubricated threads are necessary when dealing with plastic surfaces so make sure this information is taken into consideration prior beginning any task! Additionally, certain materials like aluminum may require additional steps such as anti-seize lubricant application in order achieve optimal clamping force; always check with your local auto parts supplier beforehand if unsure about what type of material is being worked with! Finally, never forget about safety equipment like gloves and safety glasses as these items can help protect you from any potential harm during your project!
Applying the Correct Type of Torque When Tightening Bolts -Torque Pressure Settings- Major Factors Influencing Settings
When tightening caliper bolts, it is important to apply the correct type of torque. This will depend on the size and type of bolt being used, as well as its material composition. It is essential to adhere to the manufacturers recommended torque settings in order to ensure proper fitment and performance. The major factors influencing the torque pressure settings include: thread pitch, thread length, bolt diameter, washer size, material strength and surface finish.
Thread pitch refers to the number of threads per inch measured on a thread gauge. A higher pitch indicates that there are more threads per inch and a lower pitch indicates fewer threads per inch. Thread length should also be taken into account when determining torque pressure settings; longer threads require more torque for proper installation. Bolt diameter is also an important factor since larger bolts require more torque for proper installation than smaller bolts. Washer size should be taken into consideration when selecting the appropriate torque pressure setting; larger washers may require more torque than smaller ones. Material strength is yet another important factor; stronger materials may require higher torques than weaker materials. Lastly, surface finish must also be considered when selecting the correct torque pressure setting; rougher surfaces typically require higher torques than smoother surfaces in order to achieve proper fitment and performance.
Heeding Special Considerations for Heavy Duty Vehicles and Off-Road Vehicles- Hydraulic Brake Systems- Adjustable Suspension Systems
For heavy duty vehicles and off-road vehicles, special considerations must be taken into account when tightening caliper bolts due to their increased weight and load capacity. Hydraulic brake systems also require special consideration due to their unique design which demands precise calibration for optimal performance. Additionally, adjustable suspension systems must also be taken into account as any changes made will affect how much torque is required for proper fitment and performance of caliper bolts.
Checking Angles when Tightening Caliper Bolts- Guidance When Replacing Prestretched Rotors or New Calipers
It is also important to check angles when tightening caliper bolts as improper angles can lead to premature wear or failure of components over time due to incorrect fitment or installation technique. In some instances where rotors have been prestretched or new calipers are being installed, additional guidance may be necessary in order to properly align components prior to making any adjustments or tightening any fasteners
Finishing Procedures After Final Assembly and Adjustment Sealing Caliper Housing ABS Motor Checks
Once all adjustments have been made and all fasteners have been tightened according to specifications, finishing procedures such as sealing caliper housing with RTV silicone sealant should be performed in order to prevent water intrusion which could lead to corrosion over time. Additionally, ABS motor checks should also be completed prior to finalizing any assembly process in order ensure proper functionality of ABS brakes if present on a vehicle model type
FAQ & Answers
Q: What are Caliper Bolt Torque Specs?
A: Caliper bolt torque specs refer to the recommended amount of pressure needed when tightening the bolts that secure the calipers. The amount of torque required can vary depending on the vehicle model year and manufacturer, as well as the type and surface of the bolts.
Q: What types of caliper bolts are there?
A: There are several different types of caliper bolts, including hexagonal head, flat head, countersunk head, and button head. Each type is designed for a specific purpose and will require a different level of torque when being installed.
Q: How do I determine my vehicle’s model year and manufacturer?
A: To determine your vehicle’s model year and manufacturer, you can use its VIN (Vehicle Identification Number) number. By looking up this number online, you can find out what year your car was manufactured and who made it.
Q: What special considerations should I be aware of when working on heavy duty vehicles or off-road vehicles?
A: When working on heavy duty vehicles or off-road vehicles there are some additional considerations to keep in mind. For example, hydraulic brake systems may require more torque to ensure proper installation, while adjustable suspension systems may require less torque in order to avoid damage to components.
Q: What finishing procedures should I follow after assembly and adjustment?
A: After final assembly and adjustment is complete, you should seal the caliper housing to ensure it remains watertight. Additionally, if applicable you should also check that the ABS motor is functioning properly before driving the vehicle again.
The torque specs for caliper bolts are important to ensure proper installation, which will help to avoid premature wear and tear on the brake system components. It is recommended that a qualified technician use a quality torque wrench when installing caliper bolts, and that the manufacturer’s recommended torque specs be followed at all times.
Author Profile
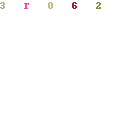
-
Welcome to Liberty Is Viral, a digital nexus where curiosity is the currency and knowledge is the merchandise. We are not just another blog on the block; we are a movement, a collective of inquisitive minds committed to the ethos of liberating information and empowering individuals.
Our journey began with a simple yet profound belief: knowledge should be accessible to all, unrestricted by barriers, free as the air we breathe. Thus, in the bustling digital landscape of 2023, LibertyIsViral.com was reborn, a revitalized platform poised to quench the intellectual thirst of discerning netizens. And we can say we are a bit successful on that, since our community is expanding by the day (20,000 readers and increasing!)
Latest entries
- March 22, 2023AppliancesThe Best 2 Inch Brass Fire Hose Nozzle for Maximum Firefighting Efficiency
- March 22, 2023AppliancesElevate Your Brand with the Best Custom Next Service Due Stickers
- March 22, 2023Lawn, Patio And Exterior5 Best Bird Netting Solutions for Protecting Cherry Trees
- March 22, 2023Apparel And JewelryFind the Best Drop Cut T-Shirt for Men: Our Top Picks