Solving the Problem of a Foodsaver Sealing Strip Not Heating – A Step-by-Step Guide
The Foodsaver Sealing Strip may require replacement if theHeat element is not working.
Foodsaver Sealing Strip Not Heating
The Foodsaver Sealing Strip is an essential component of any FoodSaver vacuum sealing system. It applies heat to the proper area of the FoodSaver Vacuum Bag or Roll, creating a secure, airtight seal. But if your Foodsaver Sealing Strip isn’t heating up, it can be very frustrating. In this article, we’ll discuss what could be causing your Sealing Strip not to heat up, and how to troubleshoot the issue to get it working properly again. We’ll also provide tips on how to properly care for and maintain your Sealing Strip in order to preserve longevity and ensure a high-quality seal every time. So if you’re having trouble with your Foodsaver Sealing Strip not heating up correctly, read on for help!
Common Causes and Solutions for FoodSaver Sealing Strip Not Heating
One of the most common issues that arise when using a FoodSaver sealing strip is that it stops heating. This is usually due to a few different factors, such as an underloaded or underpowered fuse, dirty or blocked air vents, or an issue with the heater element. To solve this issue, first check the fuse to make sure it is not overloaded or underpowered. If the fuse appears to be fine then check the air vents for any blockages. If all looks okay then inspect the heater element itself, making sure there are no faults with it.
Possible Reasons for FoodSaver Sealing Strip Not Responding
Sometimes the FoodSaver sealing strip may not be responding, even when powered on and the temperature set correctly. This could be due to a faulty temperature sensor or a locked control panel lockout feature. To diagnose this issue, first check if the temperature sensor is working correctly by testing its output voltage with a multimeter. Then check if there is any lockout feature enabled on the control panel which may be preventing the sealing strip from responding correctly.
Replace Parts to Fix FoodSaver Sealing Strip Not Working
If after checking all of these factors and none of them seem to be causing an issue then you may need to replace some parts in order to get your FoodSaver sealing strip working again. The two main components that could need replacing are the temperature sensor and circuit breaker/fuse. To replace these components you will need to carefully unscrew them from their respective positions and replace them with new ones before reassembling everything back together again.
Safety Concerns Before Replacing Parts for FoodSaver Sealing Strip Not Heating
When replacing parts for your FoodSaver sealing strip it is important to take certain safety measures in order to ensure that no damage is done during installation or use afterwards. When unscrewing cables make sure you do so carefully and never force anything as this could cause damage or even electric shock! You should also ensure you handle any soldering iron safely while connecting new components as they can get very hot during use and cause damage if handled incorrectly.
How to Check Unusual Sounds from FoodSaver Sealing Strip?
If your FoodSaver sealing strip starts making unusual noises then it could signify an underlying problem that needs attention before further use of your product. In order to diagnose this issue, make sure you maintain a constant noise level by listening closely while running the sealer at various temperatures and speeds. If you hear anything out of the ordinary then inspect the thermal protector capacitor as this could indicate an electrical fault which needs attention before further use of your product can occur safely again.
Steps to Troubleshoot FoodSaver Vacuum Sealer Not Working Properly?
Troubleshooting a FoodSaver vacuum sealer can be a difficult task if you dont know what to look for. To ensure that you get the best results from your appliance, its important to know how to identify and address any issues that may arise. The first step in troubleshooting a FoodSaver vacuum sealer is to check the sealer lid alignment. If the lid is not properly aligned, it can prevent air from being properly evacuated from the bag, leading to an ineffective seal. Additionally, its important to inspect the LED status lights for error codes or other indicators of trouble. If any lights are flashing or showing an error code, this can provide valuable insight into what may be causing your vacuum sealer not to work properly.
Diagnose Malfunctioning of Electrical Components in FoodSaver Machines?
When diagnosing malfunctioning electrical components in your FoodSaver machine, its important to reset any GFCI outlet tripped circuit breaker that may have been tripped due to a power surge or other fault. Additionally, check for corroded terminal connections and replace them if necessary. A malfunctioning connection can prevent electricity from flowing correctly through your machine and make it difficult for your appliance to work properly. Finally, check the voltage stability at the power inlet port and test the internal circuit boards with a multimeter if necessary.
Guidelines To Identify Worn-out Parts Of FoodSaver Vacuum Sealer Not Working?
Identifying worn-out parts on your FoodSaver vacuum sealer is essential for ensuring that your appliance continues working as efficiently as possible. Begin by checking the voltage stability at the power inlet port; if there is any fluctuation in voltage here then this could indicate an issue with either your wall outlet or with some internal wiring inside of your machine. Additionally, test all internal circuit boards with a multimeter and look for any signs of wear or damage; if you find anything then you should replace these components immediately before continuing with further troubleshooting steps.
What Are The Precautions For Repairing Problems Of FoodSavers At Home?
When attempting repairs on a FoodSaver at home, its important to take certain precautions into account in order to ensure that everything goes smoothly and you dont end up creating more problems than you solve. Firstly, examine any issues within right environmental conditions; too much moisture or heat can cause components inside of machines like these to malfunction so make sure there are no sources of either nearby when attempting repairs. Secondly, avoid overheating by keeping away from heat sources such as stoves or ovens; this can cause serious damage both externally and internally so always make sure that everything stays cool while conducting repairs on your appliance at home.
FAQ & Answers
Q: What are the common causes and solutions for FoodSaver sealing strip not heating?
A: Common causes for FoodSaver sealing strip not heating include underloaded or underpowered fuse, dirty or blocked air vents, and heater element problem. Solutions include replacing the temperature sensor, taking out the old circuit breaker and fuse, and resetting the GFCI outlet tripped circuit breaker in order to diagnose malfunctioning of electrical components.
Q: What are the safety concerns before replacing parts for FoodSaver sealing strip not heating?
A: Before replacing parts for FoodSaver sealing strip not heating, it is important to take certain safety precautions such as unscrewing cables carefully and handling soldering iron safely.
Q: How to check unusual sounds from FoodSaver sealing strip?
A: To check unusual sounds from FoodSaver sealing strip, it is necessary to maintain optimum noises level and inspect the thermal protector capacitor.
Q: What are the steps to troubleshoot FoodSaver vacuum sealer not working properly?
A: Steps to troubleshoot FoodSaver vacuum sealer not working properly include checking the sealer lid alignment, inspecting LED status lights for error codes, checking voltage stability at power inlet port, testing internal circuit boards with multimeter.
Q: What are the precautions for repairing problems of Foodsavers at home?
A: Precautions for repairing problems of Foodsavers at home include examining issues in right environmental conditions and avoiding overheating by keeping equipment away from heat sources.
The conclusion is that the Foodsaver Sealing Strip is not working properly if it is not heating up. This could be due to a variety of factors such as a faulty power cord or a malfunctioning heating element. The best course of action would be to troubleshoot the issue by checking the power cord and replacing any faulty parts as necessary. Additionally, if the issue persists, contacting customer service or returning the product may be necessary.
Author Profile
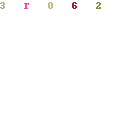
-
Welcome to Liberty Is Viral, a digital nexus where curiosity is the currency and knowledge is the merchandise. We are not just another blog on the block; we are a movement, a collective of inquisitive minds committed to the ethos of liberating information and empowering individuals.
Our journey began with a simple yet profound belief: knowledge should be accessible to all, unrestricted by barriers, free as the air we breathe. Thus, in the bustling digital landscape of 2023, LibertyIsViral.com was reborn, a revitalized platform poised to quench the intellectual thirst of discerning netizens. And we can say we are a bit successful on that, since our community is expanding by the day (20,000 readers and increasing!)
Latest entries
- March 22, 2023AppliancesThe Best 2 Inch Brass Fire Hose Nozzle for Maximum Firefighting Efficiency
- March 22, 2023AppliancesElevate Your Brand with the Best Custom Next Service Due Stickers
- March 22, 2023Lawn, Patio And Exterior5 Best Bird Netting Solutions for Protecting Cherry Trees
- March 22, 2023Apparel And JewelryFind the Best Drop Cut T-Shirt for Men: Our Top Picks